Foam Jacking Problems
Foam Jacking can lead to many problems in attempting to raise concrete in Regina.
There are better and safer options.
There are better and safer options.
- Cavities & Voids… Most concrete slabs overlay a significant void condition that must be filled prior to being able to raise the concrete slab. Voids are commonly found along a foundation, due to the consolidation of loose backfill used when the foundation was constructed. This settlement zone can be as much as 18 inches, or more, which would require a large volume of foam to do the job correctly. Filling such voids and cavities is beyond the capability of foam that simply sets up too fast to properly fill any sized void.
- Costs… A simple question to pose is…what jacking material costs more, polyurethane foam or mud? The answer to this question explains why it is important to get a comparable Mudjacking price, and not simply accept the faulty premise promoted by the foam jacking company, that foamjacking is less costly than Mudjacking, when it is many times more costly.
- Cost example… On a Gunner LiftCrete estimate to raise the customer’s patio, driveway, the walk to the front step, and fill the cavity under the front step, the cost was $2,500.00. The customers had also received a foamjacking estimate on the same areas for a shocking $9,000.00, minus front step fill. This cost variance is effectively robbery.
- Appearance… A foamjacking company will also mislead a customer into a false believe their foam injection process is less damaging because they use access holes at half the diameter of the Mudjacking access holes. What they fail to advise is that they require twice as many holes, and even more…because foam is non-flowable and hardens in 5 seconds. Mudjacking access holes are 4 to 6 feet apart and can be finished to closely match the existing surface, or can be imprinted. Furthermore, the larger diameter Mudjacking holes allow for monitoring for proper void filling below the slab, something foamjacking completely neglects.
- Experience… is important to ensure the settled concrete slab is properly supported during the raising process, which is critically important to both methods, if unnecessary damage and proper elevations are accomplished. Mudjacking in Regina has been raising concrete slabs for now 40 years, by Gunner LiftCrete, whereas foam jacking is a new process that has only been advertized as a concrete slab raiser over the last couple years. Basically, foamjacking will always be a trial-and-error process that will never survive the test-of-time necessary to acquire any slab raising expertise. Foamjacking has been a bad idea from the start, and based on its history foamjacking will always be a bad idea.
- Control… a big issue with raising concrete slabs, because foam sets in 5 seconds there is no ability to carefully nudge the slab into position, which Mudjacking does permit with material that is flowable during the project. Foamjacking has a tendency to leave a slab under jacked or over jacked an over-steering due to the quick solidification of the foam. Rarely is a foam jack slab ever raised to original elevations, simply because the injection process is too erratic, uncontrollable, and subject to trial and error guesswork.
- Cavity Fill… Does foam completely fill all cavities? From foam jacking installation videos, it is clear the foam product has difficulty exiting along the edges or up through cracks and construction joints, which proves the foam jacking process results in uncontrolled pillow formations with a surrounding cavity. This type of formation is not conducive to proper structural support or in damming off water migration that prevents it from ponding under the slab or undermining the adjacent foundation.
- Stops Water… Mudjacking uses a clay-base material mixed with cement and water to create a grout like material that completely fills the large cavities as well as the tapering cavity created by raising the slab, which is necessary to withstand heavy vehicles, and acts to seal the underside of the concrete slab preventing wet/dry and freeze/thaw slab shifting, creating slab stability. This is an important feature Mudjacking provides and foam jacking pillows do not.
- Important Condition… Often a cavity under a front step must be filled prior to raising the adjacent front walk. Otherwise the ground around the step will slough-in to undermine the front walk’s support. Any lifting of the walk will be short lived. This step cavity typically requires 2-3 cubic yard of material, something impossible for foam jackers, but an easy fill for Mudjackers.


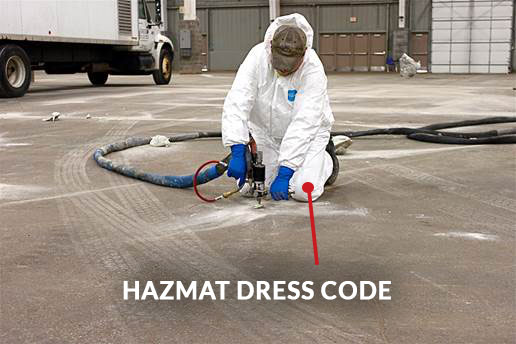
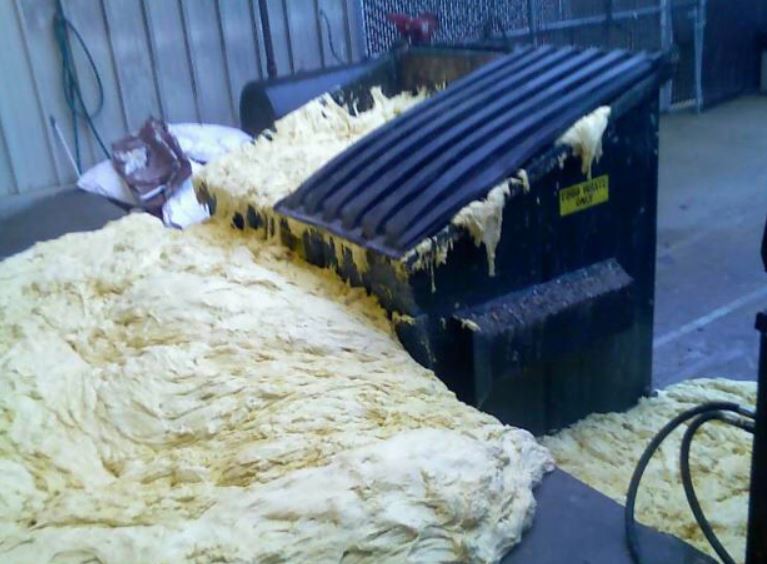
- Touch-Up Requirements… There is a possibility the ground under a mudjacked concrete slab will dry and settle, requiring a later Mudjacking touch up. When this occurs with a Mudjacked concrete slab, the former access holes can be re-used and the slab can be adjusted to very fine increments. Whereas foam expansion does not have fine control and will easily exceed the required adjustments. The guesswork involved with quickly expanding foam is a major control issue associated with all foam applications.
- Health Issue… The clay-based Mudjacking materials can be re-used as landscaping fill, whereas polyurethane foam cannot be re-used or recycled, and must be disposed as a hazardous material, not unlike asbestos.
- Rodents & Insects… Foam jacking fails to block out rodents and insects, these critters can simply burrow into and through the foam material. In fact the warmth of foam insulation will encourage such an infestation. Contrary to Mudjack material containing cement, this grout like material will obstruct rodents, and insects, to completely barrier off areas, under steps and crawl space grade beams.
The above describes only a few of the polyurethane foam jacking disadvantages that must be seriously considered by property owners deciding to raise their settled concrete slabs. Comparisons between Mudjacking and foam jacking will clearly show a foam product is not the right approach to properly filled and universally supported concrete slabs, when long-term reliability is required.